{{serverconnectlatestnews.data.showlatestnews.data[0].news_title}}
{{serverconnectlatestnews.data.showlatestnews.data[0].news_date.formatDate("d MMM yyyy")}}
{{serverconnectlatestnews.data.showlatestnews.data[0].news_teaser}}
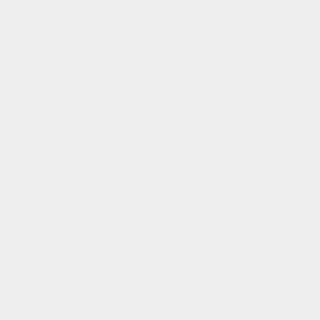
The Normanton Plant is a facility capable of melting and casting various metals and alloys, primarily steel alloys. The primary function is the production of quality steel for research and development projects as well commercial quality ingots and continuous cast billets and slabs. Assay melting of clients scrap and revert melting of highly alloyed metals using electric arc and induction melting furnaces is also carried out.
Using an electric arc furnace and sand casting facilities unusable scrap materials are converted into a product that can be recycled back at source.
High alloy revert melting involves the clients supplying the material in a form suitable to charge to the Electric Arc Furnace. This is melted and cast into sand moulds. Each casting box can produce eight 250kg round ingots. Samples of the molten metal are taken and supplied to the client. The cast ingot weights vary between 220kg to 250kg and are 340mm diameter.
Assay melting involves the client supplying the material (usually steel scrap) in a form suitable for charging to the Electric Arc Furnace. This is melted and then poured directly in to casting boxes. In addition to the cast metal weight, slag generated from the process is weighed and the fume dust collected by the EAF extraction system also weighed. This allows the delivered weight of material to be compared with the produced weights. Steel, slag and fume analysis are done to provide a comprehensive Assay service to the customer.
The Normanton Plant and its equipment is used extensively for Research and Development projects.