{{serverconnectlatestnews.data.showlatestnews.data[0].news_title}}
{{serverconnectlatestnews.data.showlatestnews.data[0].news_date.formatDate("d MMM yyyy")}}
{{serverconnectlatestnews.data.showlatestnews.data[0].news_teaser}}
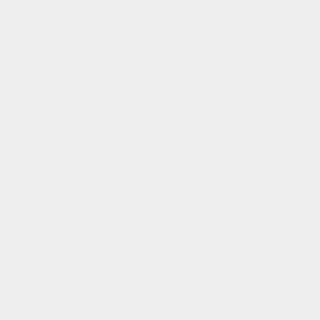
Figure 1 Operator screen
Figure 2 Slopping indication
The Materials Processing Institute had previously developed a system for detecting high-temperature steel and slag emissions, commonly known as “slopping”, from the Basic Oxygen Steelmaking furnace (BOS) to give the operators early warning to take controlling action.
The Institute had identified the need to update the approach, and subsequently re-examined the requirement and has developed a new more supportable system, capable of interfacing with existing plant CCTV camera networks.
This was achieved through in-house expertise in both the Sustainable Industry Group and Digital Technologies Group at the Institute.
To develop an Optical Based system to detect unwanted high-temperature process emissions in real time, enabling operators to take corrective action to reduce emissions to the environment, reduce process waste and clean-up costs, and to improve productivity.
As well as being capable of delivering the slopping detection, the system needed to be easy for plant technical and IT people to support and maintain.
The Digital Technologies Group investigated the available open-source computer vision libraries. OpenCV, a modular design scheme was selected as the basis of a desktop prototype system, utilising a laptop’s standard camera.
Having demonstrated the success of this approach a standalone CCTV camera was used to develop a new prototype which has been commissioned and tested successfully on a 7t pilot scale electric arc furnace in the Institutes’ Normanton Plant, and was able to identify hot material from the furnace in real time.
The system increases process efficiency by enabling the operators to reduce slopping events, thereby minimising atmospheric emissions and process waste.
The system was developed in the industry-standard Microsoft C# general-purpose high-level programming language and is supplied with the relevant system design documentation in Microsoft Word.
The new system replaces LabView with a .NET based system.
When positioned in plant, the system gives an overview of the area of interest to the operator, plus a view on the current alert status – Figure 1.
The view on the left is the camera view. The red polygon is the field of interest (this is operator configurable). The monochrome image to the right shows the pixels which have been “triggered” in the field of interest.
Figure 1 Operator screen
Once the plant starts to operate the system continuously records and monitors both the camera view and the field of interest, and once the operator threshold is breached an alert is shown on-screen, and a notification is sent to the plant process control computer to indicate that the plant is currently slopping – Figure 2.
Figure 2 Slopping indication
As can be seen on the camera image to the left of Figure 2, there is considerable flaring in the field of interest due to slopping activity. The monochrome image clearly shows heightened activity in the field of interest and displays on the screen the words “HEAVY SLOP”. The system, as well as alerting plant process control systems, has the capability to trigger an audible alarm if necessary.
The Materials Processing Institute has the expertise to develop bespoke computer vision systems to support operators in making timely process control actions, using off-the-shelf components and standard, well established software development environments.
The Institute can develop these systems rapidly, using open source libraries and standard CCTV cameras. This capability is transferable to other CCTV and imaging applications, including the potential use of cameras operating in the infrared range and potential use with other (non-CCTV) imaging devices.
Enquire about services, facilities, and expertise.