{{serverconnectlatestnews.data.showlatestnews.data[0].news_title}}
{{serverconnectlatestnews.data.showlatestnews.data[0].news_date.formatDate("d MMM yyyy")}}
{{serverconnectlatestnews.data.showlatestnews.data[0].news_teaser}}
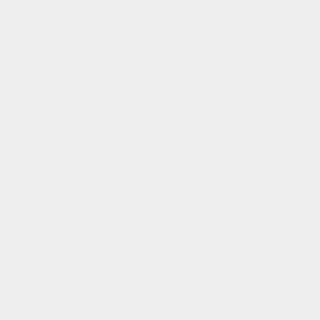
Sample bar showing defect
Light Optical Microscopy
Defect shown with Light Optical Microscopy x50
Scanning Electron Microscopy and Energy Dispersive Spectroscopy
Scanning Electron Microscopy
Defect shown with Scanning Electron Microscopy
A drilled and machined steel bar sample with a large defect that ran longitudinal to the rolling direction needed to be assessed to accurately determine the depth of the defect penetration and any particles present in the defect.
Analysis was carried out in the Advanced Materials Characterisation Centre at the Materials Processing Institute using Light Optical Microscopy, Scanning Electron Microscopy and Energy Dispersive Spectroscopy techniques. The Advanced Materials Characterisation Centre is a national and international centre for steel and metals characterisation and investigation, including failure analysis and forensic analysis. The Centre also carries out materials research, development, and innovation.
Light optical microscopy is a widely used technique for imaging and studying materials. This microscopy technique uses visible light and a system of lenses to magnify and show fine details of objects that are otherwise not visible.
Light optical microscopy was used to determine both the depth of the defect and to provide an initial assessment of what the defect was made up of.
With the magnification of the microscope set at x50 the depth of the defect penetration was shown to be 379 μm. The microscope magnification setting was then increased to x200 which showed that the defect was composed of individual oxide particles.
More detailed analysis was then undertaken which included both Scanning Electron Microscopy and Energy Dispersive Spectroscopy.
Scanning Electron Microscopy (SEM) is an analysis technique which obtains information about composition and topography of an object by scanning its surface to create a high-resolution image. SEM uses a focused beam of electrons to do this. The resulting images show information about what the object is made of and its physical features.
Energy Dispersive Spectroscopy (EDS) is an analytical technique used to determine the elemental composition of a sample. A high-energy electron beam or X-rays focused onto the sample causes the sample's atoms to emit characteristic X-rays. The measured X-ray energies are used to identify the elements present in the sample. The intensity of the X-ray peaks can also provide information about the relative concentrations of the elements.
Scanning Electron Microscopy and Energy Dispersive Spectroscopy confirmed the initial findings that the particles embedded within the steel sample bar defect were oxides; these scanning techniques also identified that the elemental composition of these oxides was predominantly magnesium oxide (MgO) based with traces of aluminium oxide (AI2O3), silicon dioxide (SiO2) and calcium oxide (CaO).
From the analysis of the steel bar using these techniques it can be concluded that the likely origin of the defect was from a steelmaking source which could include steelmaking slag, tundish slag, refractory, or re-oxidation products.
The absence of elements flourine (F), sodium (Na), and potassium (K) in the oxide compositions suggest that entrapment of the casting mould powder was probably not the origin of the defect.
Enquire about services, facilities, and expertise.