{{serverconnectlatestnews.data.showlatestnews.data[0].news_title}}
{{serverconnectlatestnews.data.showlatestnews.data[0].news_date.formatDate("d MMM yyyy")}}
{{serverconnectlatestnews.data.showlatestnews.data[0].news_teaser}}
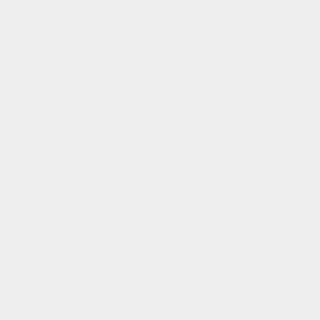
A project looking at reducing gas use and carbon emissions through waste heat recovery in the brick and steel industries.
The project has received funding from Innovate UK under No. 50790
The project involved companies from the UK steel and brick making industries with the aim of exploring ways of recovering waste heat and making furnaces more efficient and therefore helping to reduce energy and carbon emissions.
The steel and ceramics sectors both use gas-fired furnaces in continuous operation at temperatures in excess of 1,000°C. Although both industries currently utilise some of the waste heat – for example, to help dry out bricks – this project explored the potential for further energy savings.
The project was led team by the Materials Processing Institute and compared a reheating furnace operated by British Steel with brick kilns operated by Wienerberger UK. They mapped the energy flows of both processes to give a clear understanding of where energy, particularly heat, enters and leaves, where it is recycled, and where it is used in further processes.
The analysis identified opportunities to utilise more of the waste heat, including:
Even modest efficiencies can result in significant fuel savings – for example, using waste heat to raise the temperature of combustion air by 40 degrees can reduce the amount of gas used by between 3–9%.
The findings of this project highlighted how these highly efficient processes might further improve and become less carbon intensive using improved heat recovery and combustion technologies. These improvements will typically be possible on all similar continuous reheating furnaces and brick kilns.
The project findings have resulted in further development by partners, with Wienerberger UK investigating waste heat ideas and British Steel exploring future combustion efficiency options. The results have also been shared more widely across the two sectors, which includes more than 40 other brick kilns and 20 steel reheat furnaces.
Dates - December 2020 – May 2021
Funder - Innovate UK
Funding - £45,000