{{serverconnectlatestnews.data.showlatestnews.data[0].news_title}}
{{serverconnectlatestnews.data.showlatestnews.data[0].news_date.formatDate("d MMM yyyy")}}
{{serverconnectlatestnews.data.showlatestnews.data[0].news_teaser}}
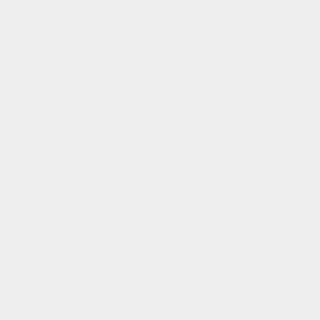
Using end of life cement as an electric arc furnace flux to produce steel, whilst also capturing the slag for use in the cement industry.
The Cement 2 Zero project has received funding from UKRI as part of the Transforming Foundation Industries Challenge
In 2018, 7.3Mt of CO2 emissions were attributable to the UK concrete and cement sector; 6.5Mt were from clinker production. Researchers at the University of Cambridge have invented a new process of clinker production which has the potential to eliminate these emissions and enable the production of zero emission cement. The vision of the Cement 2 Zero project is to demonstrate this innovative process on an industrial scale for the first time.
As the UK moves towards net-zero by 2050, the aim of the Cement 2 Zero project is to utilise steel recycling using an Electric Arc Furnace (EAF), to produce clinker for cement production. This project will produce 20 tonnes of cement clinker via this innovative process.
Portland Cement, the most common cement worldwide, has similar characteristics to Electric Arc Furnace (EAF) flux. Our research has proven that Portland Cement can be made from recycled cement in an EAF during the steel recycling process. The Cement 2 Zero project will demonstrate, on an industrial scale, the production process for Cambridge Electric Cement and its utilisation in a construction project in the UK.
Described by Tarmac's Innovation Director as "the most exciting option for future cement", Cambridge Electric Cement is the world's first potentially zero emissions cement made by recycling used cement in a symbiotic process with steel recycling (Electric Arc Furnace). Existing methods of reducing cement emissions rely on supplementary materials, whilst these strategies reduce emissions, they cannot eliminate them entirely as a proportion of Portland Cement is still required. In contrast the Cambridge Electric Cement process does not make supplementary material, Cambridge Electric Cement can directly replace Portland Cement, enabling zero emission cement production.
Not only will this transform cement production, but it will also diversify, expand and improve steel recycling, and reduce process emissions. If UK steel recycling expands to process the 11Mt of steel scrap collected annually in the UK, Cambridge Electric Cement production could meet 25% of UK cement demand. There are currently no other options available for producing cement without emissions.
Cement 2 Zero will investigate both the technical and commercial aspects required to successfully commercialise the process. This will involve techno-economic assessment, life cycle assessment, the construction of a prototype crusher for concrete disaggregation, and installation of a novel slag cooling system. 20 tonnes of CEC will be produced in an Electric Arc Furnace at CELSA, which will be evaluated for its use in a UK construction project. Cement 2 Zero brings together expertise from the Materials Processing Institute, the University of Cambridge and the complete supply chain including Tarmac, CELSA, Balfour Beattie, Atkins and Days Aggregates.
Using the EAF to recycle cement to reduce waste, energy, and emissions is a novel cross-sector technology adaption and the process has been proven and patented by the University of Cambridge (patent application: 2110292.6). This innovative industrial demonstrator will enable a significant step-change in cement production, the most important, prevalent, and CO2 emitting construction material. The project enables co-production of two critical materials, steel and cement, via one near zero emissions process, transforming a waste by-product of steel recycling into a valuable material.
Dates - August 2022 - August 2024
Sponsor - Innovate UK
Project Value - £6,744,540
Funding - £3,282,672