{{serverconnectlatestnews.data.showlatestnews.data[0].news_title}}
{{serverconnectlatestnews.data.showlatestnews.data[0].news_date.formatDate("d MMM yyyy")}}
{{serverconnectlatestnews.data.showlatestnews.data[0].news_teaser}}
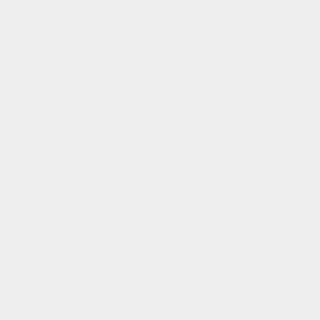
Application of Industrial Digital Technologies to the Metal Sector.
As part of the UK government funded PRISM programme of research and innovation for the UK steel and metals sector, the Materials Processing Institute is conducting research into the application of industrial digital technologies at its Normanton steel plant.
Dates - April 2021 - Ongoing
Sponsor - Innovate UK
The fourth industrial revolution, or Industry 4.0, is revolutionising the way companies operate through the use of Industrial Digital Technologies (IDTs). These include: the Industrial Internet of Things (IIoT); robotics; automation; additive layer manufacturing; artificial intelligence and analytics; simulation; augmented and virtual reality, and cloud-based platforms. So-called Smart Factories are proliferating but these usually involve digitisation using new equipment. In the foundation industries, there is a huge amount of legacy equipment with minimal connectivity.
As part of the UK government funded PRISM programme of research and innovation for the UK Steel and Metals sector the Materials Processing Institute is conducting research into the Application of Industrial Digital Technologies at its Normanton Steel Plant. The Institute is investigating the use of Augmented Reality (AR), Machine Learning, Industrial Internet of Things, new sensor technology and blockchain technologies to optimise the process and realise energy and CO2 savings. The objective is to create a showcase for the application of these technologies for the Steel and Metals sector by creating a demonstrator in a working steel plant, showing how all the associated challenges of applying Industry 4.0 technologies to brownfield sites can be overcome.
For the first stage, the project was split into several areas:
Industry 4.0 Digitisation of the Normanton Steel Plant at the Materials Processing Institute
Dr Alan Taylor