{{serverconnectlatestnews.data.showlatestnews.data[0].news_title}}
{{serverconnectlatestnews.data.showlatestnews.data[0].news_date.formatDate("d MMM yyyy")}}
{{serverconnectlatestnews.data.showlatestnews.data[0].news_teaser}}
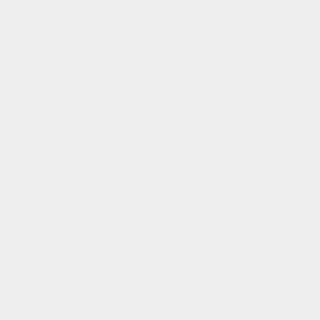
This course is aimed at personnel who are commissioning modelling work or who are interacting with the modelling process.
The course considers why we process model looking at different modelling techniques and the key steps within experimental modelling and computational fluid dynamics. It describes what validation is in modelling and why it is important and gives guidance on how to assess outcomes from modelling work for application to live scenarios.
On demand and instant access to the full course consisting of three modules.
To maximise learning it is recommended that each module is completed in sequence.
The full course consists of three modules which should be taken in sequence in order to complete the full course.
Module 1 introduces the two main fluid modelling techniques: experimental modelling and computational fluid dynamics, including important steps and assumptions in the technique set up process which are built upon throughout the course. Included in this module is an overview of why we process model, the challenges involved in process modelling and an introduction to the importance of validation.
Module 2 looks at a case study of a past piece of project work where a customer implemented a plant change from a SEN refractory supplier’s modelling which results in detrimental changes to the plant process. The Institute was asked to provide an independent review of the changes and identify what had gone wrong. The case study looks at two assumptions made during the modelling process and the impact this had. To protect customer confidentiality the data has been normalised with trends shown, but not the specifics.
Module 3 builds upon the learning from the first two modules to give you hints and tips to review modelling work you have commissioned and the extra step to take if the modelling work was unsolicited. The module starts with a brief example of measurement consistency, which is equally applicable to experimental modelling and plant measurements, with an example from tundish modelling to illustrate the point.
The course is relevant for anyone commissioning modelling work and interacting with the process.
Fluid flow modellers beginning their career would specifically benefit from module 2 learning from modelling failure.
3 x 40 minute modules
Chris Smith MEng (Hons), MSc, CEng MIMechE
Principal Researcher
Materials Processing Institute
Chris Smith is a Principal Researcher for the Materials Processing Institute. He graduated from the University of Liverpool where he achieved a Masters of Engineering (Hons) in Aerospace Engineering and went on to complete a postgraduate Masters of Science in Management.
Chris joined Corus RD&T in 2008 and has since worked on industrial and steel related research and development. During this period, he has achieved Chartered Engineer status with the Institution of Mechanical Engineers. Chris is an expert in fluid modelling, using both experimental modelling and computation fluid dynamics and leads project work modelling the fluid flow over a range of ironmaking, steelmaking and casting equipment.
Enrol for the full course, or go through the modules separately (to maximise learning it is recommended that each module is completed in sequence).
$40.00 discount available when you purchase the three modules together.