{{serverconnectlatestnews.data.showlatestnews.data[0].news_title}}
{{serverconnectlatestnews.data.showlatestnews.data[0].news_date.formatDate("d MMM yyyy")}}
{{serverconnectlatestnews.data.showlatestnews.data[0].news_teaser}}
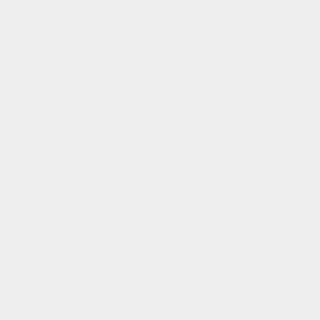
By taking this course you will learn how to prevent casting machine breakouts and save potentially huge amounts of money for your company.
Casting Machine breakouts are one of the major events on any Steel plant because of the costs involved and the potential savings in many areas. As many of these breakout events are either not examined in detail, or not fully understood, then the principal contributing factors and root causes are not clearly defined and the event reoccurs. This can incur significant costs through loss of productivity and yield, machine damage, subsequent deterioration of quality and delaying customer orders.
This course looks at many of the principal types of casting machine breakouts and details a standardised methodology that can be applied to any breakout event to arrive at a root cause and reduce these costs. For each type of breakout the causes and preventative actions are defined. Applying the learning will allow a clearer understanding of the reasons for a particular event to put into place lasting solutions. This will reduce the annual breakout rate with a significant impact on reducing costs and improving productivity. A reduction of one breakout has the potential to save in excess of £100,000.
To maximise learning it is recommended that each module is completed in sequence.
Full Course
(save $40)
$185.00
Module 1
Breakout Assessment Methodology and Entrapped Non Metallic Breakouts
$75.00
Module 2
Sticker and Starter Type Breakouts
$75.00
Module 3
“Off Corner”, “Arrested Teem” and Miscellaneous Type Breakouts
$75.00
The course consists of three modules which should be taken in sequence in order to complete the full course.
Obtain a detailed understanding of a standardised methodology to use in any breakout event. This will enable type and causes to be assessed and preventative actions to be implemented. This has potential for significant savings in many areas.
A detailed understanding of the reasons for “Entrapped Non Metallic Breakouts” and methods for prevention will be presented. The content of this module should enable most plants to see a significant reduction in this type of breakout with big cost benefits and improved productivity.
Details of the different causes for “sticker” and “starter” type breakouts are presented. The different factors involved are discussed and key areas of focus are highlighted. As sticker type breakouts are the most prevalent type on most casters, particular emphasis is placed on this.
Preventative measures are presented - These can be put in place to prevent a reoccurrence of each of the breakout types.
An understanding of this detail for “sticker” and “starter” type breakouts in this module combined with the methodology described in Module 1 should enable most plants to see a significant reduction in both of these types of breakout leading to significant cost benefits and improved productivity.
The different causes for “Off Corner” and “Arrested Teem” type breakouts are presented. Influencing factors are discussed for each type and preventative courses of action are discussed. Preventative measures to provide lasting solutions are also presented. Other miscellaneous types of breakout – e.g. Hydrogen, End of Cast and mechanical breakouts such as loss of mould oscillation are discussed, along with causes and preventative actions.
As with previous modules, an understanding of this detail for “Off Corner ”, “Arrested Teem” and other types of breakouts, combined with the methodology described in Module 1 should enable most plants to see a significant reduction in breakout rates in these areas leading to significant cost benefits and improved productivity.
Because of the significant impact of this topic on everyday Steelmaking this course will benefit a wide range of disciplines from trainees/graduates through to management in technical, production and engineering areas.
3 x 40 minute modules
David Bruce BSc. Degree in Physics (Newcastle University)
Steel Consultant
David Bruce has worked in the Steel Industry for 51 years having joined R&D in 1969 as a graduate. He worked for 20 years in the Research Dept. Steelmaking and Casting areas before moving to the Continuous Casting plant at Tata Steel, Teesside Works as Technical Manager on both bloom and slabcasters.
David has extensive knowledge and experience in all aspects of steelmaking and continuous casting production and quality (from ULC automotive grades to high carbon steels) and machine enhancement. He also has detailed knowledge of process, product and customer issues.
Latterly, David has provided expertise and consultancy for several international steel companies before moving back to the Materials Processing Institute.
Tony Parkinson BMet (Hons), DMS
Strategic Account Manager
Materials Processing Institute
Tony’s background has been predominately managing plant technical departments, in ironmaking, steelmaking and casting on different integrated steelmaking sites and has developed an in-depth understanding of the process and metallurgical interactions throughout the value chain. From raw materials purchasing decisions to the effect of those raw materials within the process right through to the overall effect on the metallurgical properties on the finished steel products.
Throughout Tony’s career, he has looked to introduce new technology and innovation into the operations and has led many significant projects from the introduction of new ferrous ores and coals to development of new steel grades like automotive, pipe grades and spring steels. Innovation on the works has been key to many of these developments projects, and often required the use of expert opinion, analysis and support from the research scientists based at the Institute. Ensuring the innovation is correctly implemented will maximise the benefits within any project.
Tony is often called to comment on the feasibility of innovation implementation within the steel industry.
Enrol for the full course, or go through the modules separately (to maximise learning it is recommended that each module is completed in sequence).
Full Course
(save $40)
$185.00
Module 1
Breakout Assessment Methodology and Entrapped Non Metallic Breakouts
$75.00
Module 2
Sticker and Starter Type Breakouts
$75.00
Module 3
“Off Corner”, “Arrested Teem” and Miscellaneous Type Breakouts
$75.00
$40.00 discount available when you purchase the three modules together.