{{serverconnectlatestnews.data.showlatestnews.data[0].news_title}}
{{serverconnectlatestnews.data.showlatestnews.data[0].news_date.formatDate("d MMM yyyy")}}
{{serverconnectlatestnews.data.showlatestnews.data[0].news_teaser}}
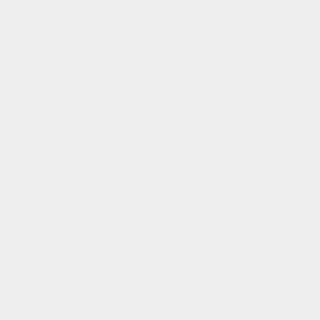
This course gives a practical and technical understanding of strand solidification to increase caster productivity and reduce quality defects.
The course is split into 3 modules:
Module 1 - Theoretical and practical understanding of primary and secondary cooling waters for optimum as cast product quality and faster casting
Module 2 - Methods used to calculate steel liquidus temperatures and the importance of accurate liquidus temperatures for reducing quality defects and increasing productivity
Module 3 - Practical methods to assess as cast product quality (sulphur prints, etch printing, surface quality and shape) to reduce quality defects.
And the learning aims are:
On demand and instant access to the full course consisting of three modules.
To maximise learning it is recommended that each module is completed in sequence.
Full Course
(save $40)
$185.00
Module 1
Theoretical and Practical Understanding of Primary and Secondary Cooling Waters
$75.00
Module 2
Methods Used to Determine Steel Liquidus Temperatures and the Importance of Accurate Liquidus Temperatures
$75.00
Module 3
Practical Methods to Assess as Cast Product Quality
$75.00
The course consists of three modules which should be taken in sequence in order to complete the full course.
Content Includes
Content Includes
Content Includes
The course covers Caster primary and secondary cooling waters, determination and importance of steel liquidus temperatures and practical methods to assess as cast product quality.
Practitioners in the Steel industry, such as scientists, researchers, technologists, technology managers and Operations and Operational management. Those who are, or who aspire to be senior leaders within the Steel industry or academia.
3 x 40 minute modules
David Stamp B.Sc.
Senior Researcher
David’s background is over 40 years in the steel industry, primarily to research and develop new technologies and innovation in both steelmaking and casting operations. This has included:
From 2001 to 2010 employed in the Steelmaking Technical Department on a 3MT a year production plant. Worked on bloom and slab casters, to improve casting practices, test new refractory products and day to day quality control of the as cast product.
At present, David is a Senior Researcher at the Materials Processing Institute, the project coordinator of a multi-national European project including comprehensive modelling, monitoring and control of solidification for optimisation of continuous casting processes.
Enrol for the full course, or go through the modules separately (to maximise learning it is recommended that each module is completed in sequence).
Full Course
(save $40)
$185.00
Module 1
Theoretical and Practical Understanding of Primary and Secondary Cooling Waters
$75.00
Module 2
Methods Used to Determine Steel Liquidus Temperatures and the Importance of Accurate Liquidus Temperatures
$75.00
Module 3
Practical Methods to Assess as Cast Product Quality
$75.00