{{serverconnectlatestnews.data.showlatestnews.data[0].news_title}}
{{serverconnectlatestnews.data.showlatestnews.data[0].news_date.formatDate("d MMM yyyy")}}
{{serverconnectlatestnews.data.showlatestnews.data[0].news_teaser}}
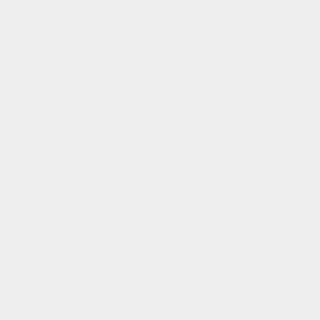
This course considers how cost savings can be made in primary steelmaking by the application of good operational and technical management.
It also includes details of how successful R&D experiments can be implemented on plant to benefit operations and add value to primary steelmaking.
The course is split into 3 modules.
Module 1: The Value of Hot Metal Pre-treatments
Module 2: The Cost Saving from Correct Scrap Selection
Module 3: BOF Vessel Process
The learning objectives are:
On demand and instant access to the full course consisting of three modules.
To maximise learning it is recommended that each module is completed in sequence.
The course consists of three modules which should be taken in sequence in order to complete the full course.
The course covers the primary steelmaking operations from hot metal leaving the blast furnace all the way through to the in-blow sample within the BOS converter. The course will discuss the operations required and provide detail where value can be added in this process by the application of R&D, strong technical knowledge and good management practices.
Practitioners in the steel industry, such as scientists, researchers, technologists, technology managers and operations and operational management. Those who are, or who aspire to be senior leaders within the steel industry or academia.
3 x 40 minute modules
Tony Parkinson BMet (Hons), DMS
Strategic Account Manager
Materials Processing Institute
Tony’s background has been predominately managing plant technical departments, in ironmaking, steelmaking and casting on different integrated steelmaking sites and has developed an in-depth understanding of the process and metallurgical interactions throughout the value chain. From raw materials purchasing decisions to the effect of those raw materials within the process right through to the overall effect on the metallurgical properties on the finished steel products.
Throughout Tony’s career, he has looked to introduce new technology and innovation into the operations and has led many significant projects from the introduction of new ferrous ores and coals to development of new steel grades like automotive, pipe grades and spring steels. Innovation on the works has been key to many of these developments projects, and often required the use of expert opinion, analysis and support from the research scientists based at the Institute. Ensuring the innovation is correctly implemented will maximise the benefits within any project.
Tony is often called to comment on the feasibility of innovation implementation within the steel industry.
Enrol for the full course, or go through the modules separately (to maximise learning it is recommended that each module is completed in sequence).
$40.00 discount available when you purchase the three modules together.